Zinc-rich Coating technology
Today, galvanizing is recognized as an advanced technology for protecting metal structures from corrosion. Galvanizing or Zinc-rich coating is a direct alternative to hot-dip galvanizing, due to its anti-corrosion properties and the interaction of zinc with metal. Galvanizing is recognized as an advanced technology for protecting metal structures from corrosion.
The Scientific production company (SPC) Corrosion Protection and Zinker LLC Moscow Russia presents the most advanced zinc-rich coating material, produced at Research Center for Anti-Corrosion Protection in Russia. Certified as a standard for a Very High C4 and High C5 corrosion category with very high durability range corresponds to more than 25 years and the high between 15 and 25 years according to UNE-EN ISO 12944 -1:2018. About Technology Read more….and about “Technical Characteristics” Read more…
The Zinc-rich coating and its anti-corrosion properties
These products contain following properties:-
-Form a stable Zn-Fe sub dispersion zone on the metal surface.
-It has the property of inter-layer diffusion.
-It retains the function of surface self-preservation and self-healing throughout the service life.
-It is characterized by sufficient resistance to abrasion. The inter-atomic distance in the zinc layer is similar to the inter-atomic distance in the zinc layer, applied by the process of immersion in the bath. The resulting protective coating is a zinc layer, containing 96% of active stabilized zinc with a purity of 99.995%, thereby forming a stable Fe-Zn galvanic compound in which Zinc acts as an anode and
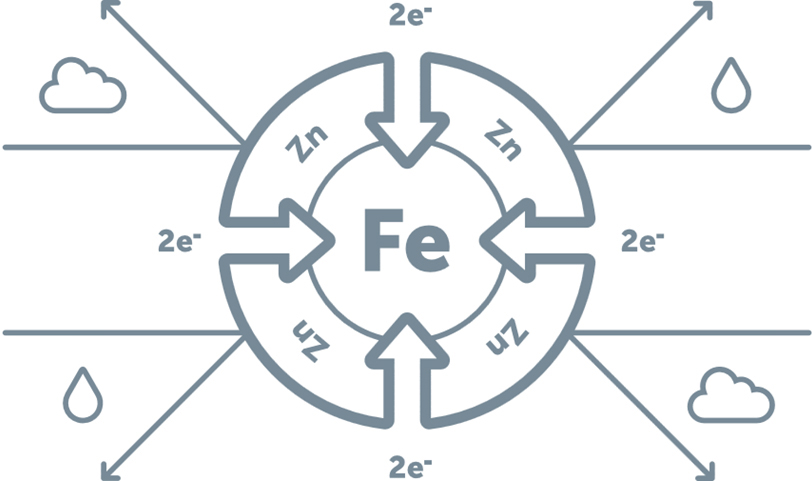
protects the ferrous metal (steel) electrochemical process, Galvanizing is the process of coating a metal (iron or steel) with a layer of Zinc to protect against corrosion by applying a zinc composition (Zinker grade composition). One-component zinc composition is applied in the temperature range from -35°C to +50°C using a brush, roller, spray or dipping.
The Production of Zinker anticorrosion compounds & Zinker-class coatings.
The zinc layer, obtained by applying the Zinker composition to a metal structure, contains 96% of active purity of 99.995%, as well as a unique polymer. In this case, the zinc deposited using this method acts as an anode that protects the iron or steel by electrochemical means. It allows you to achieve the maximum degree of adhesion and provide reliable protection of the metal from corrosion for many years.
According to a number of tests, when used in moderate and cold climates, Zinker coatings maintain the service life of structures for at least 25 years. Coating is thin-film zinc coating that protects effectively ferrous metals against corrosion.
It has superior protection properties and high adhesion to metal surfaces. Coating is elastic, resistant to vibration and shock loads and abrasion, and functions within the temp. -60°С to +150°С (for a short time, up to +180°С to +210°С during application of powder coatings. The Coating ensures simultaneous active (cathode) and passive (barrier) corrosion protection The coating is intended for anti-corrosion protection of surfaces of industrial equipment and metal constructions installed outdoors and indoors.
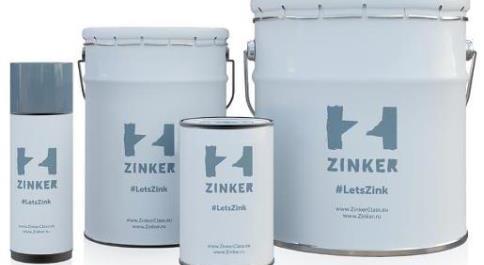
Difference from analogues
Zinc plating, unlike zinc-filled coatings (cold galvanizing), does not require overlapping finishing layers, thanks to a unique patented polymer that provides cathodic protection of zinc throughout its life. It is used as an independent coating, by analogy with hot-dip galvanizing, but, if necessary, can be used as a primer for various coatings and fire-retardant materials. It is not destroyed by UV radiation. Zinc plating, in contrast to hot dip galvanizing, is used to protect large-sized, hollow, thin-walled, lap-welded products.
Zinc-rich coating (Zinker-class coating) Properties
Zinc-rich coating is a thin-film that protects ferrous metals effectively against corrosion it has superior protection properties and high adhesion to metal surfaces. The coating is elastic, resistant to vibration and Shock loads and abrasion, and functions within the Temp.-60°С to +150°С (for a short time, up to +180°С to +210°С during application of powder coatings coating ensures simultaneous active (cathode) and passive barrier) corrosion protection. Coating is intended for anti-corrosion protection of surfaces of industrial equipment and metal constructions installed outdoors and indoors constructions installed outdoors and indoors.

The coating is not resistant to petrol and several other organic solvents; therefore, it should be covered with a medium- resistant top coating.
Zinker-rich coatings protect major industries like:

Bridge structures- and Industrial and civil engineering
Hydraulic structures- Small architectural forms – Agriculture- and more

- Shipbuilding and ship repair
- Repair of galvanized surfaces-Weld processing
CERTIFICATIONS & CONCLUSIONS
1) Conclusion ISO 12944 C5 high
The samples used, designated as “Zinc composition (composition of Zinker class, TU 2312-001-61702992-2009)”, comply with the requirements of the UNE-EN ISO 12944-6:2018 standard for the corrosion category “Very high level C4” and “High level C5” A very high level corresponds to a service life of at least 25 years, and a high level from 15 to 25 years according to UNE-EN ISO 12944-1:2018.
2) Protection of building structures from Corrosion
Protection of building structures from corrosion” came into force, where galvanizing technology is recommended as one of the methods of protecting load-bearing structures made of carbon and low-alloy steel from corrosion. In addition to this, changes have been made to the sections relating to the protection of installation welds and joints, where galvanizing technology is also recommended to us.
3) Conclusion “Moscow Scientific institute of “construction steel named after“Melnikov “
The coating system has withstood 225 test cycles according to method 6 of Russian standard. Based on the results of accelerated climatic tests, with acceleration coefficient equal to 41 for operating conditions, the predicted service life of the system in an open industrial atmosphere in a temperate and cold climate is at least 25 years.
4) Conclusion of the Russian Maritime Register of Shipping
Zinc-filled coatings based on a zinc composition (TU 2312-001-61702992-2009) on carbon steel in aqueous environments (sea and fresh water) and atmospheric conditions are not inferior in protective ability to or superior to hot zinc based on test results using accelerated Corrosion-electrochemical methods.
5) Conclusion Central scientific Institute of Corrosion & certification Moscow
Zinc-filled coatings based on a zinc composition (TU 2312-001-61702992-2009) on carbon steel in aqueous environments (sea and fresh water) and atmospheric conditions are not inferior in protective ability to or superior to hot zinc based on test results using accelerated Corrosion with electrochemical methods.
Update on Specialized Trade Fair activities Zinker-Rich Participation
QUALITY CONTROL-TRANSPORTATION -GUARANTEE

Quality Control
Anti-corrosion work is controlled both during separate operations and after the entire work has been completed. Control quality by visual inspection. The coating after polymerization should be free of through pores, blisters and visible defects. The coating thickness is controlled with thickness gauges after drying.

Elimination of defects and coating repair
Eliminate immediately all defects (scaling, blisters, etc.) occurring during application of the coating and when it is used. Dress the defect with sand paper, digrease and dry.Prepare the surface and apply the anti-corrosion coating according to the application process. The coating thickness on a metal surface is checked with a thickness gauge.

Transportation and storage
Zinc-rich coating can be transported by all kinds of transport in closed transport vehicles according to cargo transportation rules in effect at each kind of transport. The material is stored in closed ventilated storerooms or under awnings at temperatures within 35°С. If the material is stored at higher temperatures, the manufacturer does not guarantee material compliance to specifications. Keep Zinc-rich coating in containers with tightly closed covers to prevent ingress of moisture, dust and other contaminants.

Manufacturer’s guarantee
The manufacturer guarantees compliance of the material to specifications, provided the consumer shall meet transportation and storage rules, and observe application instructions. The material guaranteed shelf life is unlimited.
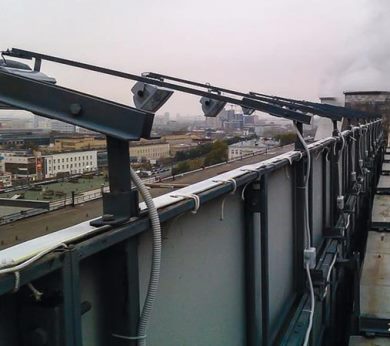
Brackets-Preparing the metal mechanically, applying the composition by air spray in 2 layers.
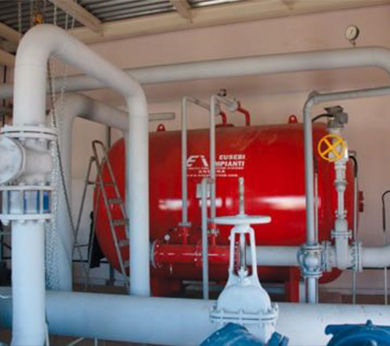
Pipeline systems-The protective coating in several layers, total thickness 100 microns, Spray gun and Brush were used
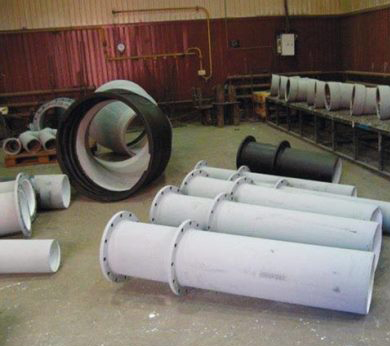
Shaped high-strength cast iron-applied with an air spray gun or a brush in 1-2 layers with a total thickness of 60-80 microns.
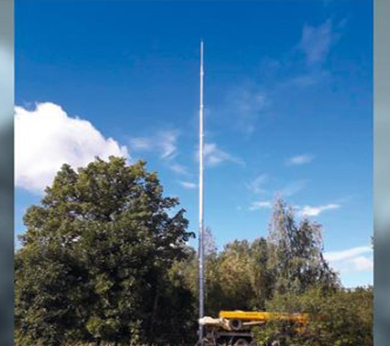
Support pipes for television and radio communications-The zinc composition is applied by airless spraying -2 layers
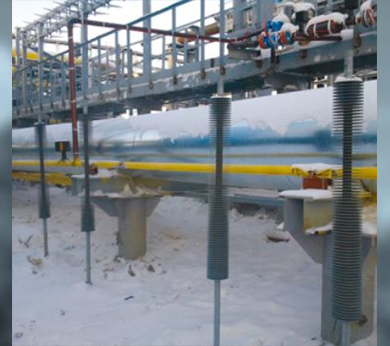
Thermal stabilizers -Application of zinc coating in 2 layers with a total thickness of at least 80 microns.