TECHNICAL CHARACTERISTICS OF ZINC-RICHCOATING
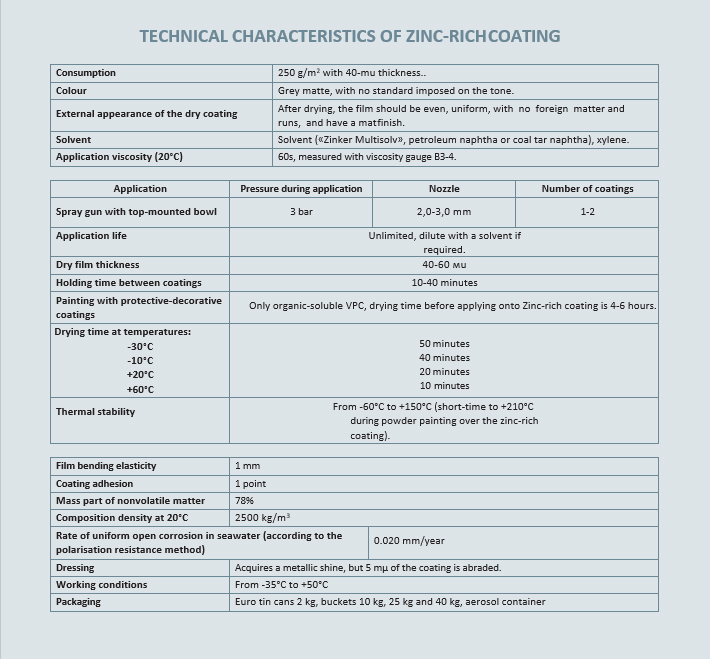
COMPATIBILITY WITH OTHER COATINGS
Zinc-rich coating composition is readily compatible with 99% of organic-soluble top coatings. It is consistently compatible with polyurethane, urethane-acrylic, acrylic, epoxy resin, vinyl chloride, chlorinated rubber, and alkyl coatings. For ideal compatibility, the holding time after application of Zinc-rich coating composition should be minimum 4-5 hours for the solvent to evaporate and not prevent adhesion in the future. The product can be used as a primer for powder paints.

The coating is not resistant to petrol and several other organic solvents; therefore, it should be covered with a medium-resistant top coating.
WORKFLOW
The workflow for obtaining an anticorrosion coating based on Zinc-rich coating composition comprises the following sequence of six operations. The anticorrosion coating workflow is recommended to be maintained at an ambient temperature not lower than -35°С. To perform anticorrosion protection operations in winter, the following conditions should be met:
ö Provide awnings or screening for protection against the elements;
ö The metal surface temperature should be no less than 3°С higher than the dew point temperature

PREPARING THE METAL SURFACE FOR APPLICATION OF ZINC-RICH COATING
All parts of an object to be protected should be accessible for inspection, preparing the surface, applying Zinc-rich coating and controlling its quality. The surface of the object to be prepared for applying Zinc-rich coating should be free of burrs, sharp edges (radius less than 0.3 mm), welding spatter, solder bulging, burns-through, and flux residue. Sites for welding metalwork (structural angles, plates, etc.) shall have no surface, clean it with detergents. The New steel (rolled stock) with tightly adhering scale shall be sand-blasted to level -2 as per applied international standards and degreased. Degrease new steel (rolled stock) with no scale.
Old rusty surface — loose rust is removed by hand or mechanically scrapers, brushes, and so forth) or with high-pressure fresh water at 10-20 МРа, followed by degreasing the surface. Previously zinc-coated surface — contaminations and the upper layer of zinc salts are removed by hand or mechanically (high-pressure water at 10-20 МРа), followed by degreasing the surface.
Previously painted surface — the paint is removed chemically and by washing (by hand or mechanically or with water under super-high pressure 175-275 МPа), followed by degreasing the surface.
PREPARING THE METAL SURFACE FOR APPLICATION OF ZINC-RICH COATING
With mechanical working of the surface with grinding wheels or sand paper by hand the abrasive grain sizes shall be within 5 to 6 as per Russian GOST 3647-71, or 180 to 220 as per the European FEPA standard. After using manual or mechanical cleaning methods.
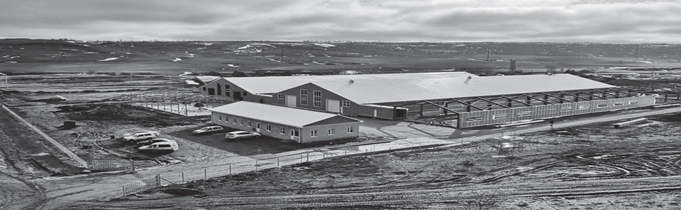
Dust should be removed off the surface without missing any areas. Compressed air for cleaning should be dry and clean, and meet the technical requirements. When degreasing small surface areas, use a brush moistened in solvents.
The working composition is applied onto a clean and degreased surface no later than in 12 hours if the metalwork was outdoors, and in 48 hours if it was indoors. Irrespective of the chosen method of application of the composition onto a prepared surface, hard-to-access welds and places should first be painted with a brush prior to applying the composition with painting equipment. If gaps and concealed cavities remain after welding, keep moisture out of these places (by any waterproofing methods that do not contaminate the surface).
Packing & Coating
Applying with an air spray gun: The equipment should be free of contaminants and earlier used VPM. If needed, Zinc-rich coating is diluted with «Zinker Multisolv», solvent or xylene to 5% of weight. The air pressure should be 0.2-0.3 МРа (2-3 bar). The nozzle diameter should be 2.0-3.0 mm.
Airless spray application: The equipment should be free of contaminants and earlier used VPM. If needed, dilute Zinc-rich coating with« Zinker Multisolv», solvent or xylene to 4% of weight. Pressure 8-12 МРа (80-120 bar). Nozzle diameter 0.015-0.025 inches or 0.38-0.63 mm.
Dip method of applying: and about «Zinker Multisolv: If needed, dilute Zinc-rich coating with «Zinker Multisolv», solvent or Xylene to 15% of weight. Zinc-rich coating can be applied onto the worked surface with a brush, roller, and spray gun or by dippingIt is used as a solvent for ZInker class compounds (and other coatings), as well as for cleaning the surface and tools. the substance or its uses are exempted from registration, the annual tonnage does not require a registration or the registration is envisaged for a later. The Chemical name of the substance “Xylene”.
Information on basic: physical and chemical properties:
- Appearance: Clear liquid
- Density at 20 ° С: 0.862-0.868 (grade A); 0.860-0.870 (grade B) g / cm3
- Flash point not lower: 23 ° C
- Auto-ignition temperature: above 450 ° C
- Concentration limits of ignition of vapors of a universal solvent mixed with air (by volume): lower – 1%, upper – 6%
Information on basic: physical and chemical properties:
Applying with a brush: The brush should be with natural bristles, and free of dust and other contaminants. There is no need to dilute Zinc- rich coating with a solvent in standard conditions.
Applying with a roller: The roller should be made of a material resistant to organic solvent and free of contaminants and earlier used VPM. There is no need to dilute Zinc-rich coating with a solvent in standard conditions.
Application with an aerosol container: When applying the composition, hold the container vertically with the valve facing up at 25-35 cm from the surface being protected. Apply at an ambient temperature of +5°С to +40°С. Having finished work, clean the valve: turn over the container and press the nozzle until clean gas is discharged. Remove composition residue with a swab moistened in «Zinker Multisolv», solvent or xylene.
The material is applied layer-by-layer, with overlapping of the edge of the earlier applied coating strip- The total coating thickness should be minimum 40 mu and maximum 160 mu. When applying onto constructions with slight mechanical deformation, the maximum thickness can be increased to 200 mu. Perform work involving application of Zinc-rich coating (except when using an aerosol container) at -30°С to +50°С and relative humidity up to 90%. The composition can be applied onto a moist surface. In this case, the surface should be free of water droplets. When applying at sub-zero Temperatures, check for absence of ice crust. It is recommended to provide an awning when applying in precipitation conditions (snow, rain).